Les Baker and Ian Ravenwood write this month’s guest blog.
Chapter 11 of my book “Fires, Farms and Forests” provides the story of how AFH and North Forest Products were instrumental in developing an industrial eucalypt plantation estate on Surrey Hills. This blog offers specific details of improved nursery techniques and the creation of a world-class nursery, which adds significantly to the Surrey Hills plantation story.
Les recalls his early years working under Dick de Boer as a plantation forester. He outlines the development of the primitive nurseries, initially set up to service a relatively small tree planting program. He describes the behind-the-scenes catalyst for change and the opportunity that arose to develop a single nursery that contained state-of-the-art equipment, and the initiative and passion of the employees directly tasked with achieving that objective.
Ian provides a detailed insight into the mind of someone tasked with a big responsibility. He outlines overseas trips to learn about modern nurseries, the lessons learned, and issues he overcame to develop a successful state-of-the-art nursery.
Les and Ian’s stories add significantly to this important history of plantations on Surrey Hills.
___________
Surrey Hills and surrounds was never an easy place to establish plantations, mostly due to cold conditions. Successful plantation establishment required all elements of development to be optimised. Otherwise, patchy or failed plantations would result. Seedling quality had to be of a high standard, and this involved some challenges as both softwood and hardwood were involved. When I joined APPM in 1980 as a plantation forester working for Dick de Boer, the technology used in both nurseries was quite primitive, servicing an annual program of about 2,000 ha.
The pine nursery was located at West Ridgley on a small, heavily sloping block of 2-3 hectares and cropped continuously for many years. Beds were formed with rudimentary equipment, and seeding was done with a primitive seeder that gave a very poor imprecise result giving significant variability in seedling size. There was some root wrenching done at the time of lifting just to make manual lifting easier. When seedlings were lifted, they were wrapped in hessian and transported to the field, all very labour intensive and costly. Cyril Hodgetts and Bob Dewar were the two nursery guys who did a great job with what they had. There was a small rustic wooded hut at the nursery entrance where the guys would sit at lunch time and hand-feed little wrens that would emerge from surrounding trees when they were called.
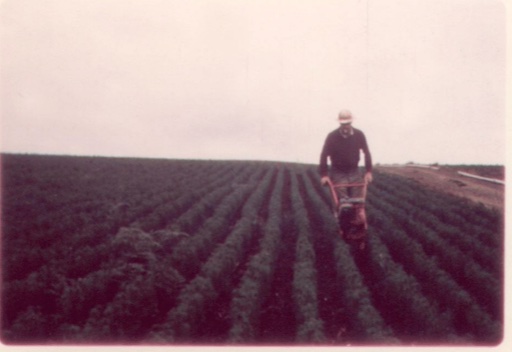
The eucalypt nursery at the Ridgley depot was equally as primitive. Seed sourced from the native stands of E. nitens was stratified to give uniform germination, then seeded onto a granite sand media in small seed trays and placed in a germination room with misting and controlled temperature. Once germinated, the seedlings, say 3cm long, were lifted and transplanted (pricked out) using tweezers into small paper pots (produced by the Lannen company of Finland). The paper pots were stretched out into a frame and filled with a media mixture of basalt soil and peat mixed in wheelbarrows. After transplanting, the paper pots were transferred onto elevated beds where they were watered and covered with paper machine felt fabric at night to protect them from frost. Most of the work here was also undertaken by Cyril & Bob together with Michael Turner, Chris Ingrahm and others as required. The transplanting was done by women mostly associated with company employees.
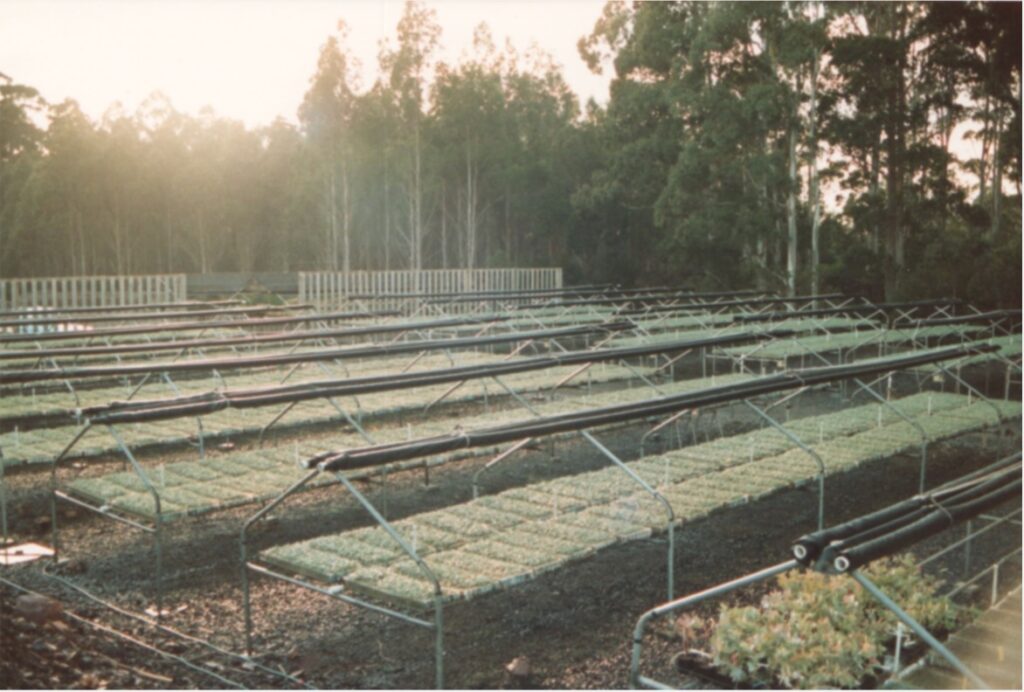
Dick had a very good understanding of the science involved in raising seedlings and did the best he could under a capital starved culture, which was about to change. There was developing an understanding in the company that the future would be more focused on plantations and less on native forest. This was promoted by the young guard of up-and-coming foresters such as David Bills, Geoff Dean, Leigh Titmus and David de Little in research. Everything changed rapidly when there was some advice given about superannuation entitlement that motivated the retirement of all the senior staff (most in their 60’s) at AFH in 1982. Another significant event that occurred not long after was the acquisition of all Wiggins Teape shares in APPM by North Broken Hill Holdings Ltd (who already were a major shareholder), which made APPM a subsidiary of North, enter the suave Managing Director Lawrence Baillieu.
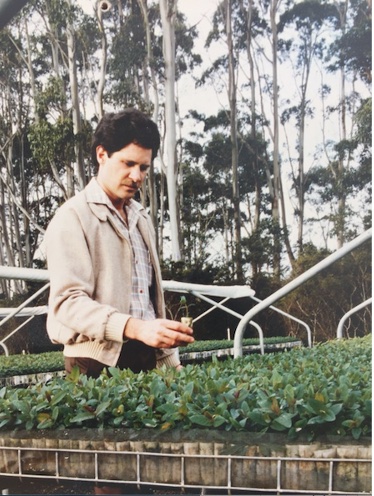
Lawrence loved Tassie and our company, its extensive landholdings, and in particular the opportunity for plantations where he gave a lot of encouragement. The Baillieu family started the Electrolytic Zinc Company and hence had their roots in Tassie. I recall the famous words of Lawrence one day when visiting the Ridgley nursery with directors: “How much plantation do you people do every year?”, he asked. After my answer he said, “well you should immediately double it and when that is achieved, double it again”. After we picked ourselves up off the floor and dusted off, we rolled up our sleeves and worked out how to do it. Lots of capex’s followed. I had the time of my life.
The first thing we did was close Tamar’s Nunamurra hardwood nursery and implemented a significant expansion of the Ridgley hardwood nursery to supply all state requirements. New beds and watering systems, media mixing facilities (large concrete mixer), roller transfer systems etc. All this made the nursery more efficient and cost effective. The genetics program for hardwood and softwood was beefed up as well.
The West Ridgley softwood nursery was closed, and a new property was purchased at East Ridgley where a potato farm was purchased; it was a perfect site. One technique adopted from the new pyrethrum industry was methyl bromide gas treatment of the soil to kill all pasture and weed seeds. It was very expensive but gave a brilliant result. A permanent irrigation system was installed, NZ Summit root pruning and bed forming equipment, spray rigs, tractor, Gespardo disk vacuum seeder, everything was new and worked brilliantly. We had the best pine seedlings with the first and subsequent crops, cost though dropped significantly. I learned from a seminar how to inoculate a new radiata nursery with symbiotic fungal spores and had some training on which puff balls to harvest. They were blended with a kitchen whizz, mixed with water and stored for use, then boom sprayed onto the nursery. It worked a treat.
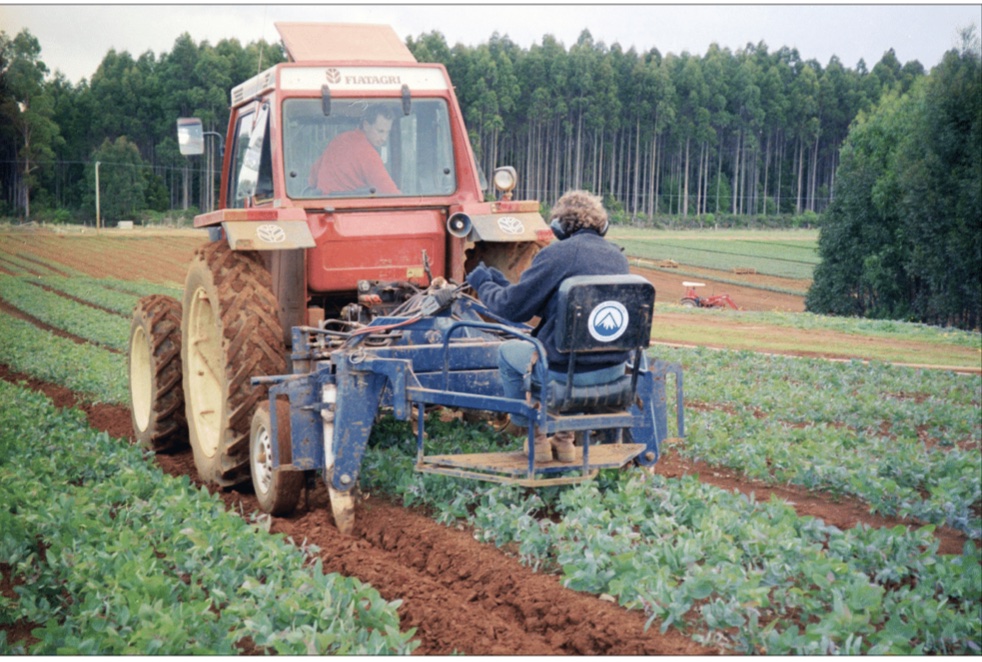
Later we developed the concept of 1/2-1/2 seedlings to provide large hardy seedlings for transplanting on the colder sites in Surrey Hills. We bought an automated vegetable transplanter that would transplant paper potted seedlings into the field nursery. When growing they had intensive topping, undercutting and root wrenching. The seedlings were very good but very expensive to produce and plant.
All the nursery production went well under these facilities for a number of years. However, the plantation program continued to expand, particularly in the east of the state. By this time, I was out of a hands-on role and working initially as manager north-west, then in Hobart head office, and later at Gunns. Ian Blanden one day suggested to me he would like to establish a state-of-the-art nursery expansion. He wasn’t going to have any roadblocks in his way. I suggested a site at Somerset that I had in mind for a number of years for such an event. Unfortunately, we didn’t own the land. Ian made enquiries and found it was owned by a Government department willing to sell, and we snapped it up in a heartbeat. Ian Blanden and Tom Fisk then went overseas to investigate the best technology and equipment for a large scale seeded eucalypt nursery, where basically none existed, just the technology for other species. The result was a fully automated pot filling and vacuum seeding line, large and automated glass houses, travelling boom irrigators, the complete works, which could be expanded on a modular basis.

I recall the opening ceremony in the mid 90’s where the Managing Director of North Ltd, Campbell Anderson came across. I put a piece of paper in his hand with the names Ian Blanden and Ian Ravenwood on it and explained that these are the only two people he needs to talk about. I had been to too many opening ceremonies in the past where the uninvolved got all the credit. I recall having a discussion with Ian Ravenwood prior to the first year’s production about hedging our bets by placing some orders with alternative providers in case of a major failure in production at the new facility, as there was a lot more than the cost of seedlings involved. Ian was very confident he could deliver top quality seedlings from day one, and he delivered an outstanding result. If it had been anyone else, I would have insisted on a backup.
After a while, Pinus radiata seedlings were produced at this nursery, and they proved to be the best performing radiata I had ever seen. At the time, we were establishing pine in the Tumut region for Gunns’ Managed Investment Schemes. The performance of the containerised pine compared to bare root in drought conditions was spectacular.
From here, Ian Ravenwood, so pivotal in the design and construction of the Somerset nursery, finishes the tale.
For the seven years before I joined AFH in 1985, I had worked in a soil and plant nutrition research group at a horticultural research centre. A lot of our work provided support to the nursery industry, particularly around issues with soil-less potting media. Skills and knowledge gained from that period were to prove very useful a decade later.
My first role at AFH was to assist in a tree improvement program for E. nitens and E. globulous, including looking at the possibility of their clonal propagation. This involved setting up a small tissue culture laboratory as well as a research glasshouse for cuttings work. Unfortunately, efficient clonal propagation of most temperate eucalypt species is difficult, and as the project to build a new single production nursery moved to a firmer basis in around 1992-93, answers were needed to the question: should it be built either as a clonal production or as a seedling based facility?
While the research group grappled with that dilemma, Tom Fisk, who was then the north-west plantation manager, and Jaap van Dorsser, a highly respect NZ authority on forest nurseries, toured South Africa and South America in 1993 to look at forest nursery operations and the technology they used. In Brazil, they saw a nursery that used multi-cell trays on a rolling bed system. They recognised that, of all the systems they had seen, it was the nursery technology that would work best in a Tasmanian context, considering the planned scale of production, the cost of labour, and the importance of minimising safety risks to employees.
Tom and Ian Blanden, the nursery manager, then visited several Scandinavian nurseries and forest nursery equipment suppliers, as mentioned by Les earlier, with a focus on the multi-cell trays and rolling bed system they had seen in Brazil. They visited two key equipment companies, Lannen in Finland and BCC in Sweden. They also visited nursery technology manufacturing companies in the Netherlands and nursery operations in Portugal, including that of CELBI.
In 1993, David de Little, our research manager, and I visited a CELBI’s newly built forest nursery in Portugal as part of a larger group on a pre-conference tour. CELBI was then part of Stora Enso, a Swedish pulp and paper group and forest owner. Our respective research groups had interacted over many years. As a result, there was a lot of overlap in what we were both doing – CELBI was mainly interested in E. globulous and, like us, had both a tree breeding program as well as a strong cuttings research program.
They were, however, a few years ahead of us in building a new forest nursery. On seeing what they had built, I could tell it was a benchmark development. They had realised that Portugal’s recent entry into the European Union would, amongst other things, herald a steep rise in the cost of labour and that they would need to build a very modern and future-proofed nursery. They had also opted to build the nursery to produce cuttings based on the research results from their small research glasshouse. The nursery used the very best of current Dutch horticultural technology to produce around seven million plants per year. It was super efficient and turned a nursery into a modern plant factory.
Engineers are much better at understanding the dynamics of scaling-up than horticulturists! As a rule of thumb, they say to increase the scale by no more than ten times the previous pilot plant. That way, unintended consequences and artefacts don’t create issues that take a lot of time and money to make good. Those who manage an annual plantation program cannot afford to not have their ordered plants available when they need them.
In that fleeting 1993 visit, I had wandered off the route organised for the tour and saw that CELBI had significant problems with survival in many of their cuttings. Millions of plants were dead or dying in their propagation houses. It must have been a logistical nightmare for all their staff that year. Plan B would not have been an easy one! Fortunately, we were part of it.
I was able to go back to CELBI’s nursery the following year. They needed to go back to seedling production methods while they grappled with their cuttings issues and were short of quality seed. We sold them a large quantity of genetically improved E. globulous seed orchard seed, and as part of that transaction, they agreed we could imbed a staff member in their nursery operation for a week or two. They also agreed to openly and fully answer all questions that were asked. By the time I arrived, the seed we had supplied had been sown, and the nursery manager (Ivone Neves) and her deputy remarked on its good performance. At that stage, a lot of CELBI’s E. globulous improvement was built around Portuguese landrace material and selections made in plantations – our improved seed was an eye-opener to the nursery. The staff at CELBI’s nursery were excellent, and I got many answers to questions prefixed with “If you were to build it again, what would you do differently”.
After my return from Portugal, I moved from the research group to the nursery manager position with a brief to maintain production from the East Ridgley and Ridgley nurseries while managing the new nursery project and its subsequent commissioning. By then, a firm commitment had been made to build a modern seedling-based nursery, and the clonal research program was ended. I was involved in the decision-making process and had absolutely no doubt it was the correct one.
Based on what had been learnt, Jaap van Dorsser, Tom Fisk and Ian Blanden had drawn up a specification that had been put out to tender as a turnkey, design and construct project. I formally joined the project as tenders were arriving. If I had come on board earlier, I might have urged a different approach (EPCM or engineer, procure, contract management), but more than 25 years later, the outcome has now stood the test of time. The successful tenderer was a joint venture of Jaakko Pöyry (a Finnish engineering firm that specialised in the forest industry), Lannen (through their Australian distributor, Transplant Systems), and the American multi-national engineering company, Fluor Daniel.
The rest is history, as they say. The nursery was built on time and on budget – not that hard to do with a ‘design and construct’ project. It has many elements that were similar to what was leading-edge in mid-1990s Dutch nursery technology, and it looks a lot like the CELBI nursery (now Altri). During my time as manager, I always considered the nursery to be a ‘factory’ – inputs, transformation and outputs. In the case of Somerset, you take a range of inputs (seed, potting mix, water, heat, sunlight) and, using established principles, transform them into an output, a plant that meets a customer’s specification. A key component of ‘factories’ are material handling systems – conveyors and the like that move the transforming product to the point of dispatch as efficiently as possible.
The operational opening of the nursery occurred soon after the contractor handed over the turnkey project in late 1996. The project had swallowed up $4.5 million of 1990s money and it needed to start earning its keep as soon as possible. The official opening was a bit of a saga. As a measure of significance of the project at the time, Federal member for Braddon, Chris Miles, organised for Prime Minister John Howard to do the opening in July 1997. Unfortunately, Howard ended up in hospital that month with pneumonia and the opening had to be postponed. There was no chance of rescheduling the Prime Minister so Chris Miles attended the official opening a month later in August. It was a grand affair with the nursery shown off in all its grandeur full of growing stock and all operations under way.
The Somerset nursery underwent at least three expansions in the following decade and, with each, the unit cost decreased significantly, and it became extremely efficient. The capital costs are high for a ‘factory’ nursery, so the fixed costs are high, but with more plants produced, they are spread further. On the other hand, the variable costs per unit are low because capital expenditure reduces the labour required. It produced around 15 million seedlings in its busiest year, although it appears to be steady at around half that now.
When I moved on from direct nursery management, I used to say that I would always look on the Somerset nursery project as my career highlight. I enjoyed solving all the problems that came with managing the project, the challenge of commissioning a greenfield site, and getting systems and staff working at their best. And most importantly, seeing the enthusiastic acceptance of its products by its customers. As time went by and I became involved in new roles, I was less certain that it was THE career highlight. But it was certainly one of them.
I have always been impressed that North Limited, as AFH’s then owner, wanted to build the very best nursery possible.To achieve that they didn’t hesitate to send front-line staff all over the world to ensure they could identify what was world’s-best-practice technology and how to get it to happen in such a relatively remote location like Tasmania.
Big thanks to Les and Ian R. for putting it into words. Great job!
Thank you Ian.
Great read. A 1st class asset that continues to underpin our industry 25 years on.
Thanks Wray.
Thanks Les and Ian for your insights and historical knowledge. The Somerset Nursery remains a critical component of Forico’s modern forestry business in 2021. Under current skilled management by Jim Wilson and Andrew Moore may it remain so for many more years to come.
Thank you Bryan. My recall is that you were in the senior role at Ridgley when the Somerset Nursery was being constructed and your support was important. I also recall your calming response to me when giving you a head’s up when we were invoiced by the contractor for more than $200k worth of variations when the project was winding up. By then the projects contingency budget component had all been spent.
Great read brings back a lot of memories of working on the Somerset site. My small role in this project was to level the site and prepare a hard stand for the project to begin. I remember walking onto the site with Ian Ravenwood and other members of the team. Ian was on crutches and after about 10 steps onto the site both crutches sunk to the hand piece. Ian was immediately in trouble.
I remember thinking this site will be a challenge but in the end it all came together.
Hi Morris, you’ve brought back some memories! Your role was vital and I recall that you even ‘invested’ a mobile phone into that hardstand. An archaeologist digging there in a few hundred years time is in for a surprise! I had clean snapped an Achilles tendon a week or so before and had a rigid plaster cast covering the full length of one leg. Fluor Daniel had just been awarded the contract and we were on-site with their team who had flown over from Melbourne to discuss the bulk earthworks (there is a story best left untold as to why North Forest Products ended up doing it on what was a design and construct contract). On that winter’s day, the site was just a very boggy and grassy paddock. I learnt that it’s not easy to unbog yourself when on crutches and one of your legs is in a full cast. I think it was you who raised a laugh from those assembled by suggesting a 4WD and a snatch strap might be the best way to haul me out. You did an amazing job getting such a difficult site levelled and gravelled and it saved my bacon with respect to the project’s overall budget. It was almost unbelievable to see fork trucks running around on that hardstand a few years later. Regards, Ian
Thanks Les & Ian for bringing back so many memories. The evolution of the nurseries from then to now is something all involved should be very proud of.
Thanks to “Mort” Bloom for highlighting Ian R’s sinking! I remember that incident very fondly, not so much for Ian though.
I also remember having a D7 temporarily stalled in forward and backwards motion on the site quite regularly. It was a challenging site but as was regularly the case, the crew came up with the answers.
Fabulous stories. They say that imitation is the sincerest form of flattery and your pioneering efforts at Somerset have been replicated by two other growers being HVP Plantations’ nursery at Gelliondale in Victoria which was completed in 2010 and now OneFortyOne is embarking on a similar project at Glencoe in South Australia.
Hi Cam, nice to read your comment. Great to see Glencoe is heading down the same path.
I enjoyed catching up with HVP’s Chris Barclay on his visits to NW Tasmania when the Gelliondale project was coming together. The first time we met I had the good fortune to be with him on an Australasian forest nursery group tour of Chile in the late 1990s and we solved many a technical question with a pisco sour (or two)!
They say that there aren’t all that many original ideas left and I am the first to say that Somerset was never one of them. Somerset was a copy of many other operations, as the story outlined. We were just so lucky to be in an era when our company enabled us to get overseas and see what could be done. Though not mentioned in the main story, we even saw similar seedling production techniques at a large celery grower’s operation near Melbourne (Schruers). I often said to others that the best way to ensure a technolgy-based project had a successful outcome was to Steal (Good) Ideas Shamelessly (SIS)!
Is Chris ‘Rosie’ Rosenthal still running the Glencoe nursery? Please pass on my regards if he is still about.
I worked at East Ridgley from 1988 with 8 women who were like absolute family to me, along with Bob, Ken and Chris and not forgetting Cyril!
I work initially in the AFH nursery and field nursery then under Gill Rasmussen in the biotech lab in the winters. I only stopped the day before I had my baby in ‘93. Then couple of years later went out to Gunns Somerset nursery, to finish up in 2004 when I got a lab job at a dairy company where it was a hell of a lot warmer than working in that cold shed where I ended up with pneumonia. I loved working out East, fond memories
Thanks for the memories Les and Ian.
I recall visiting West Ridgely nursery with Dirk, Les and Geoff Dean in 1982. There was one dead seedling on the ground and Dirk made a point of telling Les to pick it up. One of the few times I ever saw Les feeling contrite! Dirk had tried to talk me out of being a forester when I was 16 and had just finished grade 10. “You’ll never be rich,” he said, “but you will have an enjoyable life.” I’m glad I stuck with it – he was right.
When Les moved to Hobart I had the honour of occupying his “office” in the tin shed at Ridgley until the schmick new labs were completed at the top end of the nursery. They were heady days for researchers with virtually unlimited budgets and lots of interesting projects to work on. David de Little, Wayne Tibbits, Ian Ravenwood and Gillian Rasmussen at NFP were joined by me, Peter Gore and Kim Badcock from CSIRO and later, Milton Savva. Ian Whyte oversaw the whole program and made sure we had a lot of fun too. Geoff Dean had moved into the pulp research space but remained a source of inspiration. Ridgley became the epicentre of world eucalypt genetics research for a while. We had visitors from France, USA, Colombia, Spain, Sweden, Portugal, South Africa, Chile, Brazil, China and many other places. There wouldn’t have been a forest geneticist anywhere in the world who wasn’t aware of what was going on at this tiny settlement at the bottom of the planet. The visitors were a who’s who of famous scientists. Lucky for me, my CSIRO masters were in Canberra, so I was left to my own devices, most of the time. It helped kick off over 30 years of world class eucalypt genetics and silviculture research at the University of Tasmania too, a program that is still going.
Hi Peter, it’s hard to believe now that Ridgley had so many visitors from around the world.
That support from head office was so important. When David de Little recruited me in 1985, he reported to David Bills who was then Executive Forester,and a great supporter of what we were doing. When David Bills moved on and ever upwards, Ian Whyte was then promoted to the Executive Forester position and, as you write, he made sure we had fun as well as being very supportive and interested in the work.
One of the consequences of all those visitors was that we built a great network of international contacts. The research manager for Celbi in Portugal, Matts Brinsberg (spelling?) from Stora, had visited Ridgley and that led directly to the interaction we had with them and its contribution to the Somerset Project.
Interesting and enjoyable times working at Ridgley for six years with so many people mentioned in this article, who did such important work for the company.
Hi Kay, absolutely everyone was important, and especially the administrative staff we had over the years. Without that support, nothing much of significance could have happened. It can be a bit cringey to say it this day and age when the meaning of words get distorted, but it takes a team to make big things happen.
Thank you Les and Ian for this great account and memories.
I recall as a young plantation forester being the first recipient of the new nursery seedlings for our operations. The difference from what we had been doing (a combination of 1/2 1/2 and container seedlings from Ridgley) was immediately apparent in the success of the plantation estate.
I remember at the time, some trepidation with the nursery on the coast and us taking some stock to over 700m in altitude on Southern Surrey, but that was quickly allayed. The ability to nutrient harden the seedlings really was groundbreaking.
The reduction in refill plantings (with the dreaded hourly rate plantation contractor payments…) was significant – but it was much more than that – the consistency in the plantations – the ability to withstand browsing, frosts etc. made such a difference in the quality of the estate from that point.
As an aside, I wonder how many visitors there have been to the nursery. In the latter years of Gunns we had anyone and everyone – bankers, investors, sustainable shareholder interest groups, numerous Companies, ENGOs, the list goes on. Staff at the nursery were always knowledgeable, polite and accommodating to these endless groups which was very much appreciated, and the nursery was always a wonderful showcase.
Thanks.